Junho, 2019 – Com a recuperação das vendas no mercado automotivo brasileiro, a cadeia de fornecedores já registra resultados positivos e está investindo para garantir o atendimento à demanda das montadoras de veículos. Um exemplo é a thyssenkrupp, que recentemente ampliou sua fábrica de eixos de comando de válvulas instalada em Poços de Caldas (MG). Pioneira na aplicação do conceito de Indústria 4.0 no país, a planta instalou uma nova linha de usinagem de tubos e já prevê mais investimentos para o ano que vem.
A unidade é responsável por produzir eixos de comando de válvulas integrados à tampa do cabeçote do motor, componente que proporciona mais eficiência ao veículo em termos de consumo de combustível e emissões, já que contribui para uma redução de até 40% no peso do motor. “Estamos investindo na localização de processos de usinagem para aumentar nossa competitividade e diminuir o lead time do produto para nossos clientes”, explica Roberval Calca, diretor da unidade Camshafts da thyssenkrupp para o Brasil, ao destacar que a planta já opera com alto percentual da capacidade de produção.
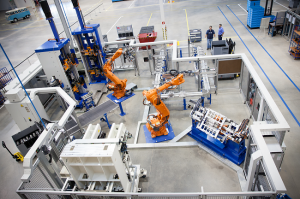
Inaugurada no final de 2015, a planta da thyssenkrupp conta com 20 robôs cujos processos estão interconectados ao longo da cadeia, e toda a linha de produção é monitorada em um ambiente virtual por meio de sensores que fornecem dados em tempo real. A unidade também está interconectada a outras fábricas da thyssenkrupp ao redo do mundo que produzem eixos de comando para o mesmo tipo de motor – uma na Alemanha, duas na China, uma na Hungria e uma no México – e é completamente adaptável e flexível.
Com esse modelo de Indústria 4.0, os colaboradores não monitoram os processos individualmente, mas sim o sistema como um todo, e a configuração das máquinas pode ser alterada a qualquer momento – com base até mesmo em novos padrões estabelecidos por meio de clientes e fornecedores ou por outras unidades da thyssenkrupp. Isso resulta em grande flexibilidade, com ganhos de eficiência, melhoria de qualidade e redução de custos.
“A interconexão entre as etapas do processo, o monitoramento em tempo real e a própria automação envolvida nos permitem obter um alto nível de controle. Isso nos deixa melhor preparados para produzir em larga escala a qualquer momento, seguindo sempre as demandas do mercado e do cliente, sobretudo no que diz respeito à qualidade do produto final”, acrescenta Calca.
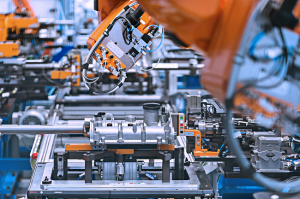
Para que essa integração ocorra, todos os elementos da cadeia de produção possuem um nome, um histórico e uma interface para a rede, e todos os componentes produzidos carregam um código com informações como número de série, número de desenho, número de peça e identificação do cliente. Dessa forma, é possível relacionar os sistemas físicos com as redes digitais de dados, constituindo então um “sistema ciber-físico” interconectado e integrado.
Esses códigos são checados automaticamente antes que qualquer passo do processo seja iniciado. Dessa forma, caso algum problema seja identificado, é possível interromper a etapa seguinte para, por exemplo, reparar e aprimorar o processo de fabricação. Além disso, a tecnologia permite uma rastreabilidade das condições de montagem de cada conjunto individualmente.
Mais detalhes acesse engineered.thyssenkrupp.com